Injection Molding
Injection molding is a method of processing resins (small pellets of plastic) to produce a variety of products, and is a cost-effective way to make a variety of high quality plastic parts.
The applications are limitless, and with PDI's 11 injection molding presses, we can make the smallest parts weighing less than an ounce all the way up to 5 lbs.
Our team of project engineers are well versed in the injection molding process, and can assist you from inception to completion of your project with us.
Example Injection Molded Parts made at PDI
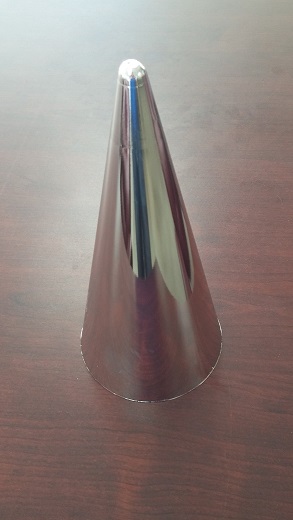
How does it work?
Injection molding has four steps: Clamping, Injection, Cooling, and Ejection.
Clamping
First, the injection molding press closes, and the mold is clamped together under very high forces. The two halves of the mold form an empty space the exact shape of your final part.
Injection
Next, the screw begins to turn which presses the melted plastic resin into the closed mold cavity. The machine injects material until the cavity is completely full.
Cooling
The resin returns to room temperature and changes from liquid to solid in the shape of the mold.
Ejection
The mold opens and the ejector pins knock the finished part out of the mold.
Image source: http://gertrude-old.case.edu/276/materials/13.htm
Injection molding is a process by which raw plastic material in the form of small pellets (also referred to as resin) is heated gently to the point where it will flow under moderate pressure. It is then injected into a mold. The mold is made up of two separable halves. After allowing enough time for the plastic to cool off, the mold opens (separates) and the molded part is removed.